While we were in Oshkosh, WI for the annual EAA convention, Lycoming announced a manditory service bulletin for about 1300 engines that had been manufactured in 2016, plus all engines that had been overhauled with new piston rods around that time. Our engine serial number was one of those listed. The inspection involved purchasing and using a special tool to find those connecting rods that may have looser than specified bearings in their upper ends.
An FAA Airworthiness Inspector friend who once owned an aircraft engine overhaul shop helped me get the job done.
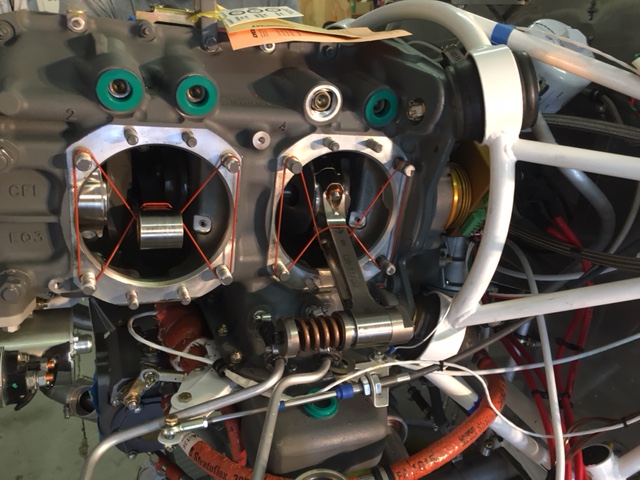
The photo shows the tool (a big coil spring attached to the #4 cylinder’s rod. If the bearing starts to slide out when the spring is compressed by six turns of its inner bolt, it fails. We were lucky all four rods passed. Note the red cylinder base o-rings that are used to keep the connecting rods from flopping around during the disassembly. The S/B was just a PITA that slowed progress by three days.