The interior of N50KB’s cowl was starting to discolor from the engine heat. 8″ wide adhesive backed foil came from Amazon. After wiping the inside with acetone I found the wide foil wrinkled during application. It was cut into 4″ wide strips that worked much better.
Application Method: Cut a strip. Remove about an inch of backing. Align and start sticking. Grab the end of the paper backing from underneath and fold it back on itself while pressing on the aluminum side with a cloth. Slowly pull the backing while pressing with my palm. Follow the fold in its travel to the end of the tape. Burnish as necessary to seal any wrinkles.
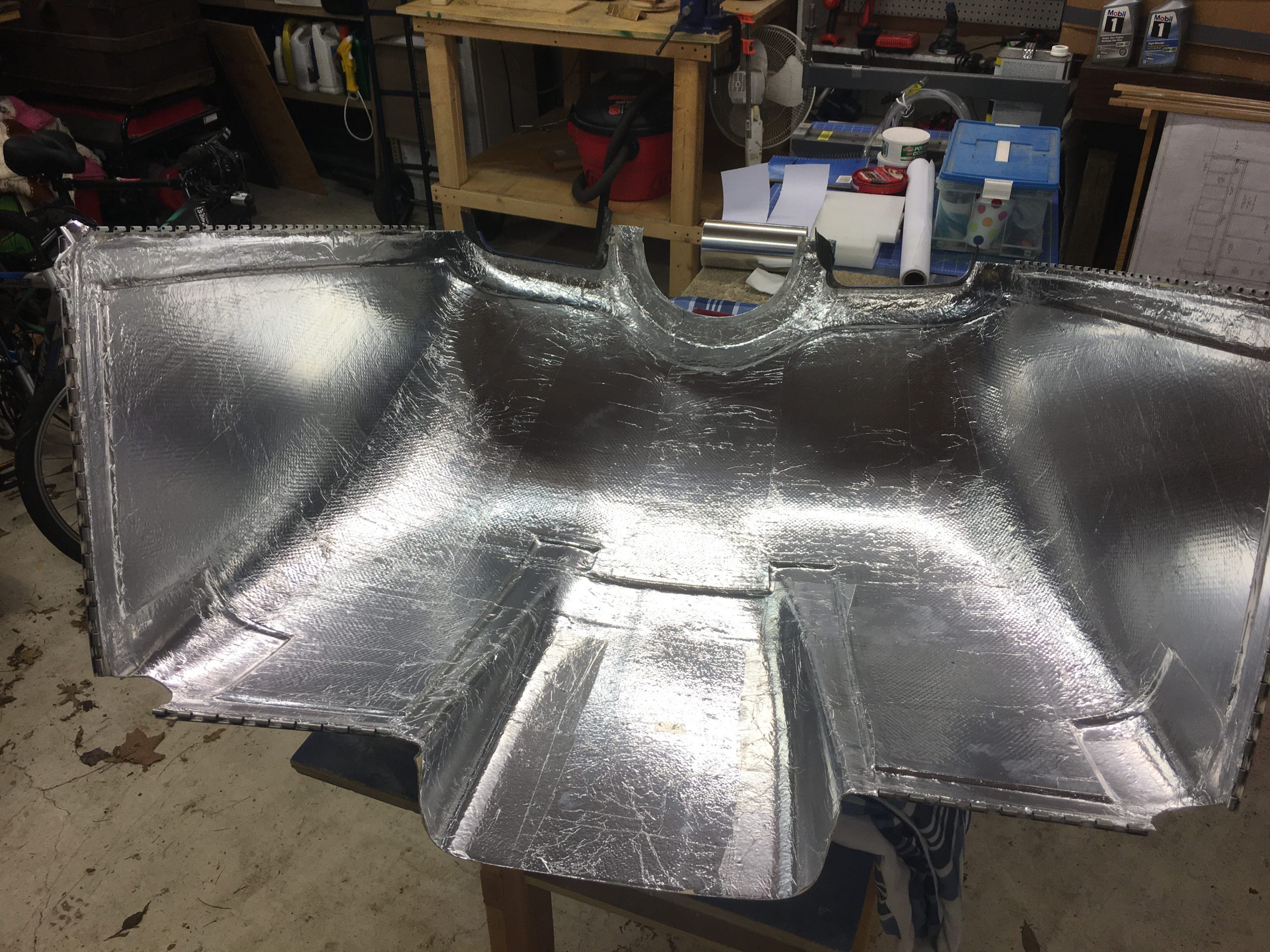